光纤快速连接器质量改进过程
1、定义阶段
在DMAIC定义阶段,需定义项目的选题依据、改进机会、改进目标、项目计划和项目组成员等。
项目依据:该公司在光纤快速连接器的两周试生产中,总共生产了10689个产品,其中有1702件产品报废,报废率为15.9%,一次通过率只有49.8%。
改进机会:当前的生产一次通过率太低,报废率太高,浪费了大量的人力物力。
项目组成员:由生产部、研发部、工艺部、质量部、设备部以及财务部共派出成员组成。
改进目标:通过365平台app下载_beat365手机客户端下载_365日博体育备用
DMAIC改进方法的实施,改进缺陷,使产品报废率降低到7%以下,一次通过率提升至80%以上。
2、测量阶段
将两周的试生产缺陷记录进行柏拉图分析,得出端面不良、干涉仪测试不过、光学测试不过为主要缺陷,占了不合格总数的90.3%,这三个流程都是测试和检测环节。因此先进行测量系统分析,正确的测量永远是质量改进的第一步。
干涉仪是干涉仪测试中会用到的主要设备,需要测试光纤快速连接器的光纤高度、顶点偏移、曲率半径和APC角度,这些测试项都需要进行测量系统分析。工程技术人员选取10个样本,3名检验员进行检验,每位检验员对每个样本重复检验3次,并将测试数据输入Minitab软件,进行Gage R&R分析,得出了干涉仪测量系统的曲率半径、顶点偏移、光纤高度以及APC角度的测量系统能力分别为8.29%、5.14%、6.89%和3.04%,这些值均小于10%,因此干涉仪测量系统满足测量系统要求。
端面检测是检测员用400倍的显微镜观察研磨后的光纤快速连接器的端面,根据看到的端面的划痕、凹点及凹陷和裂纹的多少和大小来判断端面质量是否符合要求。由于端面质量主要由检测员通过目视进行检测,该测量系统属于属性值测量系统。工程技术人员选取55个样本,由2名检测人员进行检测,每名检测人员对4个样本重复检测2次。样本既包括合格品,不合格品;既包括明显不合格品或合格品,又包括介于合格与不合格之间的产品,即样本涵盖了整个生产过程的产品范围。将测试数据输入Minitab软件,进行属性值Gage R&R分析,分析结果如表1所示。
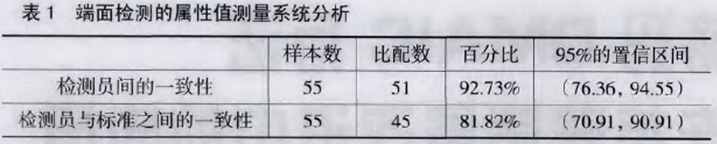
从表1可以看出,测量系统的匹配百分比为81.82%,达到了测量要求。
光学测试是测试员将成品光纤快速连接器插入光学测试仪,然后读取测试仪输出的插入损耗和回波损耗,测试结果完全取决于光学测试仪,而光学测试仪在每次使用前都会进行校准的,因此是可信的。
3、分析阶段
结合前面阶段得知的造成成品率不高的3个主要缺陷,通过仔细研究光纤连接器的生产流程和操作手册,发现干涉仪检测和端面检测都是对研磨工序的检测,而测量系统是可信的,因此,研磨工位的质量缺陷应该是造成整个光纤连接器成品率不高的最主要原因。
研磨是指使用端面研磨机对光纤快速连接器端面进行打磨和抛光的一道工序,用端面研磨机对光纤端面打磨和抛光的过程有4个步骤,涉及D30um、D9um、D1um和SONG4种型号的研磨片。研磨出的端面的质量几乎决定了光纤连接器的性能,因此研磨环节是光纤快速连接器生产过程中最精密也是最核心的步骤。但是在实际生产中研磨工位影响因素众多,而且各因素并不完全独立,因此项目组决定采用头脑风暴法,并绘制因果图对人、机、料、法、环各因素进行逐一分析,如图1所示。

根据因果图,并利用FMEA方法(Failure Mode and Effect Analysis),对各种影响因素进行评估,项目组最终确定了两个影响光纤快速连接器报废率高的主要因素,作为改进的重点:
①光纤连接器半成品尺寸偏小。
所谓光纤链接器的半成品,是将固化好了预埋光纤的陶瓷插芯和插芯基座压接在一起所形成的半成品。经过随机抽样测量,发现有41%的光纤连接器半成品尺寸比正常的尺寸小,这个尺寸偏小会导致研磨的时候研磨压力不够,形成APC角度偏小、曲率半径过大和端面划痕、裂纹。
②研磨片使用次数过多。
研磨片使用次数超限后,会导致研磨片的性能发生变化,可能引起各种不可预知的问题,包括端面的划痕、凹点及凹陷和裂纹,干涉仪测试中的不规则曲率、APC角度偏小、顶点偏移。
4、改进阶段
在经过分析阶段确定了关键的少数影响因素之后,需要针对这些因素来进行验证和改进。
①光纤连接器半成品尺寸偏小的改进。
光纤连接器半成品是由陶瓷插芯和插芯基座压接而成,现分别对陶瓷插芯外径尺寸和插芯基座内径尺寸做假设检验(假设检验的结果见表2)。 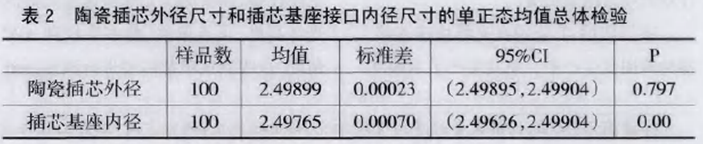
a、陶瓷插芯外径尺寸的假设检验(标准尺寸为2.499±0.0005mm);
H0:这批陶瓷插芯的外径尺寸为2.499mm ;
H1:陶瓷插芯的外径尺寸不是2.499mm;
b、插芯基座内径尺寸的假设检验(标准尺寸为2.49±0.01mm);
H0:这批插芯基座的内径尺寸为2.49mm;
H1:插芯基座的内径尺寸不是2.49mm。
从表2可以看出,陶瓷插芯外径尺寸的P=0.797>0.05,所以接受Ho假设,认定这批来料的陶瓷插芯的外径尺寸是2.499mm;插芯基座接口内径尺寸的P=0.000<0.05,所以拒绝H0假设,认定这批来料的插芯基座接口的内径尺寸不是2.49mm。
由此看来。插芯基座接口的内径尺寸偏大是根本原因,其内径尺寸95%的置信区间是(2.496,2.499),这个区间虽然在正常的尺寸范围内,但是偏离了中心。在压接过程中,压接的压力是根据陶瓷插芯2.499mm和插芯基座接口内径2.49mm的标准设计的,如果插芯基座接口的内径全部偏大,而遇上陶瓷插芯外径偏小的情况,在同样的压力情况下,就有可能将陶瓷插芯压力更深,导致光纤连接器半成品前部突出尺寸过小,最终的结果可能会导致在研磨的时候压力过小,研磨成品不合格。
对于这个问题,最终解决办法是:
a、通知供应商,要求供应商改进尺寸,重新供货;
b、在产品线增加一个测量环节,测量光纤半成品的突出尺寸,根据研磨治具的尺寸,这个光纤连接器半成品的前端尺寸定为9.5±0.05mm。
②研磨片使用次数过多的改进。
在研磨过程中有4种型号研磨片,只有4个步骤都结束后才能对光纤连接器进行参数测量,因此采用交叉排除验证法。交叉排除验证法的基本思想是,在保证其他3种型号研磨片不会超限使用的前提下,对剩下的这种型号的研磨片进行极限测量,通过采集的参数画出图表就可以直观的看出所针对的这种研磨片的最佳使用次数。以SOHG研磨片作为第一个改进实例,在保证其他3种型号的研磨片不会超限使用的前提下,对SOHG研磨片进行极限测量,图2是经过5次测量实验后得到的数据图。
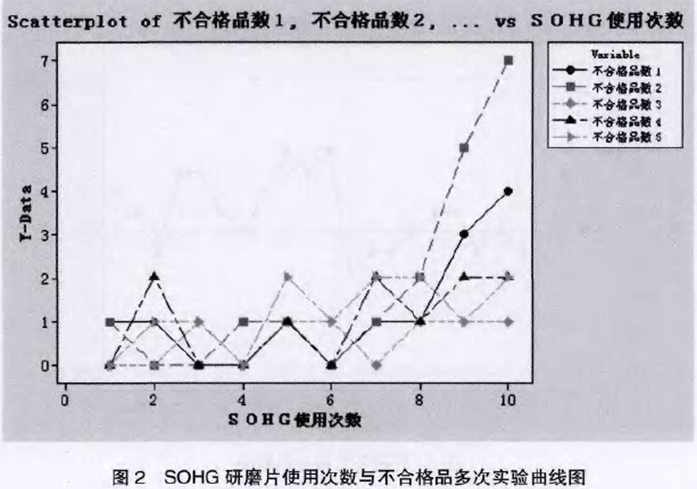
经多次实验,大部分SOHG研磨片都可以使用10次而不会影响成品质量,但有些SOHG研磨片在第9次出现了不合格品上升的拐点,考虑到批量生产,实验实际上将SOHG研磨片使用次数定为8次。
基于同样的方法,可以依次得到所有4种研磨片的最大使用次数,通过多次排除检验,最终得到4种研磨片的最大使用次数,即D30um为50次,D9um为30次,D1um为50次,SOHG为8次。
5、控制阶段
控制阶段需要有效控制影响响应输出的关键影响因子,实现预防性控制。项目组将改进阶段得到的措施用于实践生产,然后监控一些关键参数,具体测量方法:
①每半小时测量5件光纤连接器半成品的前端尺寸,连续测量25组数据。将采集得到的数据绘成Xbar-R控制图,光纤连接器半成品的控制目标为尺寸范围9.5±0.05mm。
②每小时抽检100件研磨成品,分别记录不合格品数量,计算不合格率,连续记录24小时,绘制计数型控制图,其中研磨成品不合格率控制目标为7%。
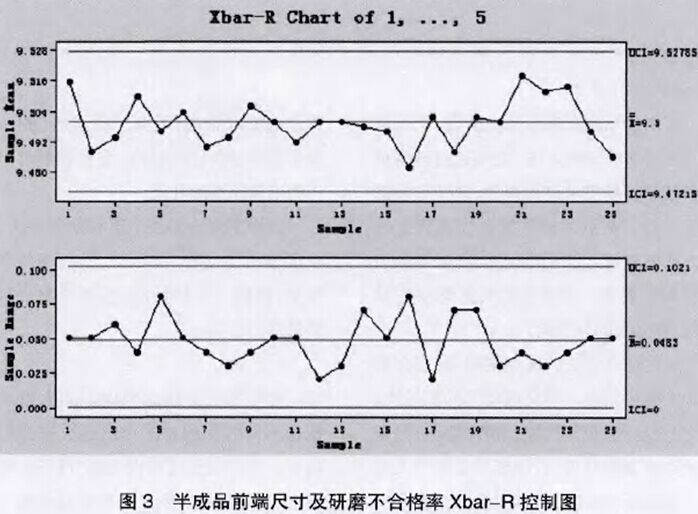

从图3和图4可以看出:所有点都在控制限内,这些点随机分布在中心线周围,并且没有链、趋势或者其他模式。
因此,当前过程是稳定可控的,影响光纤快速连接器质量的两项主要缺陷在改进后得到了很好的控制。